[China Packaging Network News] color box in the die-cutting, bonding and packaging process burst angle, popping problems often plague many packaging and printing companies. Let's take a look at how the senior technicians deal with this type of problem.
1, caused by improper pressure burst
1.1 There is foreign matter in the creasing groove of the bottom plate, which leads to a sharp increase in pressure during die cutting. This is a common cause of bursting in production and is also a destructive cause. It will cause the entire dark line to break and cause the product to be scrapped.
1.2 run version, ie die-cut version or bottom version, so that the steel wire falls outside the creasing groove. The burst caused by this reason is mainly concentrated on the dark line in the same direction, because the cutter or the indentation knife does not fit tightly with the wooden formwork and is deflected under the pressure condition.
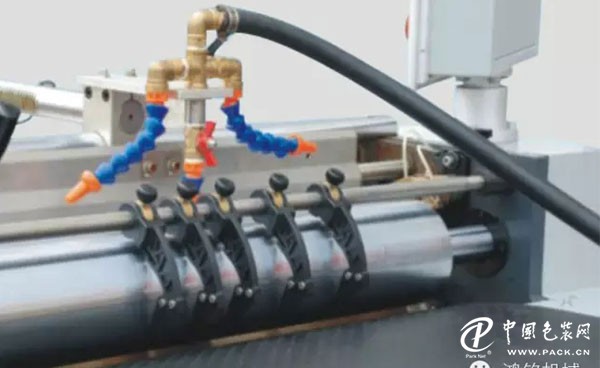
1.3 The thickness of the steel wire and the width of the indentation bottom slot do not match the material of the paper. According to the requirements of the die-cutting process, different steel wires and different thicknesses of the bottom plate and different dark groove widths should be selected for different papers. If they are not matched, it is easy to cause the dark lines to burst.
2, die-cut production process caused by the burst
2.1 When making a die-cut version, the position of the steel wire is improperly handled or burrs are left when the steel wire is cut off. In the die-cutting process, if the product is surface-treated, it is covered, for example. The burrs left on the steel wire during die-cutting will damage the tensile strength of the surface film. When the product is molded, the film cannot be subjected to stress and bursts will occur.
2.2 The knife steel wire at the dark line has a knife edge and an interface. Because the interface is not smooth, tearing occurs during die cutting.
2.3 When the position of the sponge pad of the knife is not proper, there will be a phenomenon of pressure line burst. The deformation and damage of the knife will also cause the pressure line to burst.
2.4 Whether the cutter and the line on the cutter die are reasonable. In particular, the thickness of the paper is not taken into consideration during design, and the knife and the wire cannot effectively avoid the overlap. When the molding occurs, the interference occurs, which causes the stress to be excessively concentrated and burst.
3, material quality problems
3.1 The moisture content of the paper is too low and the paper becomes brittle. This phenomenon occurs more often in winter. Due to the cold and dry weather in winter, the relative humidity in the air is relatively low, which directly affects the moisture content of the paperboard, resulting in cracking of the paperboard after pressing. Generally, the moisture content of the base paper is controlled at the upper limit (8%). -14%);
3.2 Paper coating material The biaxially oriented polypropylene film is slightly chipped, resulting in reduced tensile strength. Lamination is a common paper surface treatment method. The main material is BOPP film. If the BOPP film is damaged before die-cutting, BOPP film can not be forced to burst due to damage after die-cut. The burst of the film occurs only in the film layer. As the stress point increases, it will extend along the burst direction, and the underlying paper will not burst. This indicates that the film has nothing to do with it. If the film is not broken, the film has no relation with the film. problem.
3.3 Paper is not correct. During die-cutting, if the indentation steel wire is perpendicular to the paper fiber direction, and the fiber of the paper is broken radially, the dark line is easy to bend, the molding is good, and the angle is small; if the indentation steel wire is parallel to the paper fiber direction, the paper is not in the transverse direction. Damaged, the dark line is not easy to bend, forming a rounded corner, a large angle, for the paper outer force, easy to break. This directionality of paper has little effect on the die-cut of sheetfed products, but it is not well formed, but it is not easy to burst the wire. However, it has a greater impact on the products of the card. If the handling is not good, not only the molding is not Well, it is also easy to burst the line, mainly the dark lines of parallel paper lines burst at different positions, and the other direction does not burst.
3.4 The wattage configuration is too high. The bursting strength and lateral crushing strength of the base paper are one of the influencing factors. If the folding paper is too low, it can easily cause a burst.
3.5 mold use time is too long. In the die-cutting, after the die-cut version is used for a long time, the crimping knife will be loosened, resulting in that the crimping knife pops up during the die-cutting process, causing the paperboard-pressing line to burst. Due to the prolonged use of the pad, the rubber pad bursts due to the unevenness of the pad.